Steady But Niche Progress in 3D Printing
Also known as additive manufacturing, the technology has found valuable uses in contemporary industry, but remains far from the general-purpose manufacturing process its names imply.

“Additive manufacturing” and “3D printing” are both terms for the process of joining materials layer by layer, through automated computer control based on computer models, to produce physical components. Specialized machines of varying sizes layer a material, typically metal or polymers i.e. plastic, to create a three-dimensional object. It holds the potential of simplifying manufacturing, with multiple machining, casting, molding, and assembly processes replaced by software-directed “printing.” This is why investors, consultants, and enthusiasts have seen and promoted it as a transformative technology for over a decade. The prestigious consulting firm McKinsey predicted in 2013 that it could have an economic impact of over $500 billion by 2025.1 These expectations have not been met. The global 3D printing market had just an estimated $13.5 billion in revenues for 2022.2 While there are functional companies and the industry continues to grow, 3D printing remains peripheral to the machine tooling market, which brought in $87 billion in 2022.3
You can listen to this Brief in full with the audio player below:
Despite being relatively small, the 3D printing industry is highly financialized, with most major U.S. printer companies being publicly-traded, and increasingly under pressure to limit investment for the sake of shareholder returns. Net income for most public 3D printing companies is generally negative, despite some having been listed before 1990. Besides the U.S. market, there are functional, privately-owned companies in Europe and a new generation of well-funded Chinese companies. Besides the primary industrial 3D printing market, there is a large market for cheap “desktop” 3D printers, primarily dominated by Chinese companies. While industrial printers frequently cost over $1 million, desktop printers can cost a few hundred dollars.4
As a manufacturing process, 3D printing has some undeniable advantages, including building complex shapes with fewer material inputs and components. However, there are challenges, including the cost of specialist printing material, quality control, and fabrication speed. As it is currently constituted, the industry will be limited to quick prototypes, repairs, and a perhaps growing list of niche uses in various manufacturing supply chains. The core conceptual promise to substitute organizational complexity in manufacturing with the technological complexity of a single machine will, however, remain appealing to manufacturers and technologists alike.
Multiple Traditions of Knowledge United Under One Marketing Term

The potential benefits of 3D printing can be understood in the context of existing methods of manufacturing components and products. Industrial manufacturing depends on a range of processes requiring specialized equipment. Casting, for example, is the process of placing a liquid into a casting die, which cools and solidifies to create a desired shape. Forging is metal manipulation through compression. Huge forge presses are required to shape ingots for large metal structures like nuclear reactor pressure vessels.5 Machining is the process whereby a desired shape is made by removing excess material and is essential to fabricating the vast majority of components found in durable goods. Machine tools range in sophistication from manually-operated mills and lathes to advanced “computer numerical control” (CNC) machines.6 The term “additive manufacturing” was coined in contrast to the “subtractive” manufacturing of machine tools.
There is no one technique behind what is called 3D printing or additive manufacturing; these are rather umbrella terms for an open-ended list of different techniques for layering materials with computer control. There are seven common and distinct processes: vat photopolymerization, material jetting, material extrusion, binder jetting, powder-based fusion, sheet lamination, and directed energy deposition. Each can also be subdivided up into several other separate techniques. For example, fused deposition modeling, the most popular form of cheap, personal 3D printing, is a form of material extrusion.
These techniques were all developed in the 1980s and 1990s by U.S., European, and Israeli engineers and researchers, who were generally able to build companies out of them. To this day, these companies are the most prominent players in the industry. Different techniques use different tools and forms of energy to connect thin layers. Some use lasers or electron beams and others use thermal heat. The essential thing they have in common is the layering of materials to create three-dimensional shapes. Printers require some form of actuation to dispense material. This can be done through linear gantry-style robotics or, in some cases, articulated robotic arms.
The first commercially-viable 3D printing technique, vat photopolymerization or “stereolithography,” was patented in 1986 by the American Charles “Chuck” Hull, a former chemical engineer at DuPont. Vat photopolymerization involves curing liquefied polymer resin material in a vat with ultraviolet light from a laser. This causes the resin to harden and create a solid layer. A platform is gradually lowered down, allowing for another layer to be placed on the preceding one, and so on. Notably, the photopolymers necessary for this process were invented in the 1950s by DuPont, Chuck Hull's former employer.7 Upon patenting the first vat photopolymerization process, Hull set up the South Carolina-based company 3D Systems, where he remains the chief technology officer today.
In 1989, another American inventor, Steven Scott Crump, patented fusion deposition modeling, a form of material extrusion.8 The same year, he founded his Minnesota-based company Stratasys. This technique involves the plastic material being deposited in layers through a heated nozzle, and the layers fuse as they are both in a melted state. Material jetting is arguably the technique most comparable to standard “two-dimensional” printing. Here, rather than the heated material being extruded layer by layer, droplets are jetted onto a build platform, cooled, and cured by ultraviolet light. Unlike vat photopolymerization, inkjets allow many different photopolymers to be used simultaneously. Like extrusion, material jetting is largely limited to polymers. The technique was pioneered by the Israeli firm Objet Geometries, which has now merged with Stratasys.
Metal 3D printing has been chiefly reliant on applying heat to melt or sinter material, with the first patent for such a concept being filed in 1972 by the French inventor Pierre Ciraud.9 For metals, the most popular form of printing is termed powder bed fusion. In 2019, 85% of metal 3D printing systems were part of this subset.10 For this technique, powdered metal is rolled from a container to a build platform that slowly descends as layers are added. A laser or electron beam fuses layers continuously.11 There are many subcategories of powder bed fusion. Selective laser sintering was first patented by Carl Deckard, a program manager at DARPA, in 1986.12 An offshoot technique, selective laser melting, was first developed at the Fraunhofer Institute in Germany. Direct metal laser sintering was developed by multiple institutes but commercialized by the German company Electro Optical Systems in 1995.13
Another method for metal 3D printing is directed energy deposition, which was developed at the U.S. Sandia National Laboratory in the 1990s.14 It involves feeding a metallic powder or wire through a nozzle and melting it with a laser. The melted material is deposited layer by layer to create a structure. It is used almost exclusively for metals and can create high-strength components with dense metallic structures. It can also achieve this at speed, with higher deposition rates than powder bed fusion, making it more viable for large structures like rocket fuselages and engine components. Its current disadvantages include the residual stresses on the materials left by the high heat of a laser, of up to 2500 degrees Celsius.15 Directed energy deposition can be used to repair components but cannot produce complex or intricate parts and is best left to large structures. In 2023, the startup Relativity Space successfully launched a rocket that, by weight, was 85% printed from such techniques. Though the rocket successfully launched, it failed to reach orbit.16
Sheet lamination, developed in 1991 by the California-based company Helisys, involves placing sheets of material on each other and binding them with an adhesive before cutting with a laser, knife, or ultrasonic tool.17 This can be applied to paper, plastic, ceramic, or metal. Ultrasonic additive manufacturing is essentially sheet lamination for metallic materials, with ultrasonic vibration removing the oxides between the sheets and thus fusing them.18 Finally, binder jetting printers deposit a liquid substance to act as an adhesive on successive layers of powdered material. It can be used for most types of materials and is a fast form of printing, but it offers weaker structural integrity.19 Metal binder jetting was developed in 1993 at MIT by two materials scientists, Emmanuel Sachs and Michael Cina. The publicly-traded Massachusetts company Desktop Metal, founded in 2015, is today's most prominent binder-jetting company.
For a manufacturer, the decision on which type of technique to use exactly is affected primarily by the material being layered, whether it be polymers, ceramics, metals, sand, paper, or composites. The potential of the industry is overwhelmingly related to polymers and metals. When choosing a specific material, multiple characteristics must be considered, including tensile strength, resistance to bending, stretching, heat, and “impact,” the tendency of a material to deform, or “creep,” under constant stress, and the tendency to deform when it is compressed.
The most common polymers used are acrylonitrile butadiene styrene (ABS) and polylactic acid, functional materials for basic prototypes. More durable polymers like nylon, and composites like kevlar and carbon fiber, offer increased strength but require more expensive printers. 3D-printed metal parts can be made from stainless steel, titanium, and aluminum.20 Currently, most revenue is still directed towards printing polymers, but the metals business is converging.21 According to one analysis, the total earnings of the polymer market are $11 billion, while for metals, they are $8 billion.22 The market for ceramic 3D printing is developing at a slower pace, with sand, concrete, and clay all being potential materials.23
Filling Real Gaps in Manufacturing

The initial and most enduring appeal of 3D printing techniques was to prototype components quickly and cheaply. A design could be uploaded, printed, subsequently tested, and reiterated. The part would then often be mass-produced through established machine tooling processes.24 This ease of use similarly applies to repairing or replacing broken parts. While traditional supply chains cannot account for out-of-stock items or components that have been discontinued, 3D printing allows for relatively easy replication of any desired shape. The use of 3D printers for quick supply of new parts is becoming common in the automotive repair industry, with many parts not being licensed.25
Perhaps the highest-profile application of 3D printing has been to manufacture rudimentary firearms with personal, hobbyist “desktop printers” for use at home. In 2012, the gun rights activist Cody Wilson set up the company Defense Distributed to popularize 3D printing of firearms, leading to a media outcry and several legal battles with the U.S. government.26 Though such firearms are considered unsafe and of poor quality, they serve as a powerful gimmick to demonstrate the technical progress in 3D printing, as well as the libertarian ambition to decentralize industrial production of firearms. Notably, Defense Distributed’s founding and initial period of controversy correlated with a period of high market valuations for 3D printing companies. Much as with drones, the useful application of a nascent technology for military purposes is seen as a way to validate its overall value.
Rather than guns, the most successful large-scale use of 3D printers has been medical. The orthodontics company Align Technology has been a significant partner of 3D Systems since its founding in 1989, using stereolithography to produce customized dental aligners. Medical-grade polymers are formed around teeth molds to create an aligner tailored to the specific shape of a patient’s teeth. The company has revenue in the billions and, over its history, has served over sixteen million patients.27 Aligners must be replaced and updated every two weeks, meaning printers produce over a million molds daily.
In 2023, Align acquired vat photopolymerization company Cubicure, indicating it is integrating development into its own business rather than relying on external suppliers.28 This is potentially bad news for 3D Systems, as this case study is by far their most successful, but it is an endorsement of the industry itself. 3D printers are also routinely used to produce the shells for millions of hearing aids, which are subsequently outfitted with electronics and acoustic vents.29 Sonova, a major Swiss hearing aid manufacturer, sells over two million 3D-printed hearing aids annually.30 These examples show how 3D printing has a clear advantage when it comes to mass-producing objects that by their nature must all be customized to unique specifications rather than standardized.
There are also cases where 3D printing has been used to replace standard mass production techniques. General Electric, a major producer of aircraft engines, has built up 3D printing capacity through multiple acquisitions.31 From 2015 to 2021, General Electric used powder bed fusion to make 100,000 nickel-alloy fuel nozzle tips for jet engines. The use of 3D printers, in this case, reduced the number of components for a fuel nozzle from twenty to one, creating a more durable and lightweight component. The fuel nozzles are not rotating parts and so have less stringent specifications. For example, the turbine shrouds used in the same engine could not be 3D-printed.32 General Electric has also used 3D printing to develop its upcoming Catalyst turboprop engine, a small engine designed for propeller aircraft. The company claims it has replaced 855 traditional components with 12 printed components.33 From a weight perspective, it is 35% 3D printed, but this does not include rotating components.34
In both aerospace and automobile manufacturing, 3D printing is increasingly common for such small and non-critical components. But current 3D printing techniques are severely limited by deposition rates, or the speed at which they can print material. Forcing through a metal wire or powder and heating it is more time-consuming than cutting a slab of metal into different components. This makes current techniques extremely uneconomical for fabricating large parts. The fastest deposition rate for metal 3D printing is the “electron beam additive manufacturing” technique developed by the defense welding company Sciaky, which can deposit 18 kilograms of titanium per hour.35 For comparison, Tesla’s pioneering “Giga Presses” for making automobile bodies have an effective “deposition rate” in the thousands of kilograms per hour.36
This does not mean 3D printing cannot be useful in building molds for said presses. Tesla is reportedly developing an upgraded Giga Press with the mold made from 3D-printed sand structures.37 Using sand structures allows the mold to be changed quickly. Should this innovation be successful, it would replicate 3D printing companies' success in creating molds for dental aligners and underscores the high utility of iteration and customization enabled by 3D printing.
The cost of materials can be a major challenge for 3D printing.38 Metals for 3D printing usually come in powder form, meaning they have to be atomized from solid metallic structures. They often cost up to eight times more per unit of weight than conventional materials.39 Other estimates claim they cost up to fifteen times more.40 High-end titanium alloy powder for printers can cost up to $500 per kilogram.41 In contrast, titanium alloy rods can be bought from Alibaba for $25 per kilogram, a twenty-fold difference.42 Because most 3D printing techniques require high temperatures for thermal energy or lasers, compared to servo motors or hydraulics for CNC machines, they consume more energy per hour.43 The precise consumption is however highly dependent on the workload. One study for 3D printing in the pharmaceutical industry shows that consumption per hour can be up to three kilowatt-hours, comparable to an industrial robot.44
The properties of 3D-printed materials still need to be fully understood. Economic studies indicate that 3D printing processes are not subject to productivity gains due to repetition because failure rates often result from the unpredictable quality of some finished products.45 In 2017, the British aerospace manufacturer and user of directed energy deposition, Rolls Royce, collaborated with the Oxfordshire-based direct light source organization to better analyze how uneven surfaces, partial sintering, cracks, and other phenomena occur during the printing of metal objects.46 The research led to better real-time defect detection.47 But anomalies related to direct energy deposition still need to be better understood.48 The traditions of knowledge behind 3D printing still need to be fully formed.
A Tumultuous and Financially Struggling Industry
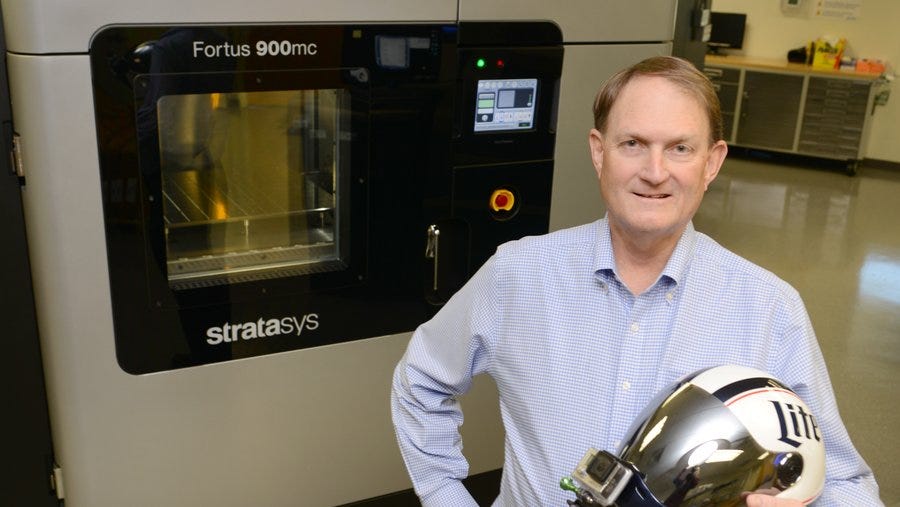
Over the last ten years, publicly-traded 3D printing companies have achieved valuations exceeding billions, only for their market capitalization to collapse. 3D Systems, the original 3D printing company, still exists with a revenue of $538 million in 2022.49 The company went public on the New York Stock Exchange early in 1988 and achieved a market capitalization of $9.6 billion in 2013 before slumping to $670 million today.50 Almost all other public 3D printing companies have had similarly high valuations fall dramatically. This collapse is in part based on the negative net income of most of the companies involved. In 2023, only one of the major publicly-traded 3D printing companies had a positive net income—of under $4 million.
But the previous valuations were heavily skewed by extremely speculative forecasts. McKinsey, in 2013, estimated that 3D printing could have an annual economic impact of between $230 billion to $550 billion by 2025.51 In 2020, another investment firm predicted 3D printing revenue could reach $120 billion in 2025.52 These figures are nowhere close to being achieved. Despite this, a specialist market research firm focused on the 3D printing industry argued global revenue could grow from a reported $18 billion in 2023 to $120 billion by 2032.53 Overly optimistic forecasts from market research firms and consultancies, in part formed by the marketing of companies themselves, has had a stimulating effect on investment on the industry, but now there are a large number of financially precarious companies that have to balance capital investment and research with placating disappointed shareholders.
Financial difficulties have led many firms to seek acquisition by larger players or merge to form a more viable industry leader. During 2023, 3D Systems, Nano Dimension, and Desktop Metal all attempted to buy Stratasys despite two of them having far less revenue. Eventually, Stratasys and Desktop Metal agreed to merge in May 2023.54 However, 79% of Stratasys investors rejected the merger, with institutional advisors suggesting a merger with 3D Systems was preferable.55 These companies, despite being diminutive, are beholden to the same pressures of institutional investors as established companies like Meta, IBM, or Amazon, despite the fact they have not yet proved the viability of their business.
The most robust privately-owned 3D printing company is arguably Germany’s Electro Optical Systems (EOS). Unlike most other ventures, it is a family business founded in 1989 by the physicist Hans Langer. In 2023, it had an annual revenue of $612 million. More importantly, the company has enjoyed profit margins of over 10% while its competitors lost money.56 Early on, Langer faced patent infringement lawsuits from 3D Systems and was forced to sell 75% of EOS in 1993 to the family-run optics manufacturer Carl Zeiss.57 In 1997, having made advances in metal sintering, Langer repurchased Zeiss’ stake. EOS’ core offerings are direct metal laser sintering and selective laser sintering, examples of powder bed fusion. Langer has been effective in getting corporate patronage in the German automobile industry, with BMW agreeing to be the first customer before EOS even had a product. Langer is by far the wealthiest founder in the 3D printing industry, with an estimated net worth of $2.7 billion.58 In 2019, Langer stepped down as CEO, with his daughter Marie Langer taking over.59
By volume, most 3D printers are sold for personal use among hobbyists or are used on a small scale by small businesses. Increasingly, this market is dominated by Chinese suppliers, located mainly in Shenzhen. In 2021, Chinese suppliers accounted for over 70% of the “desktop” 3D printing market, meaning about 1.5 million of the 2.2 million sold that year were Chinese.60 The most notable Chinese startup here is Bambu Lab, founded by Ye Tao, a former engineer at the massively successful Chinese drone company DJI. Tao spent over seven years at DJI, rising from product management to becoming the director of propulsion. All of Tao’s executive team are also former employees of DJI. Formed in 2020, Bambu Lab has earned a similar reputation for high quality at market-altering prices. The company ran one of Kickstarter's most successful hardware-based crowdfunding campaigns, raising over $6 million.61
Chinese producers have commoditized smaller 3D printers and are becoming more competitive in developing larger industrial printers. X’ian Bright Laser Technologies is the largest, with $120 million in revenue for 2022.62 It is in the metal manufacturing space, with 70% of its business in China’s aerospace industry. Another major 3D printing company, Farsoon Technologies, had revenue of $64 million in 2022.63 BLT, Farsoon, and a handful of smaller companies are publicly-traded on the Shanghai Stock Exchange. Between 2017 and 2020, the Chinese central government pushed a “3D action plan.”64 However, 3D printing has not gained patronage to the degree of semiconductors, robotics, or spaceflight.
The Core Promise of 3D Printing
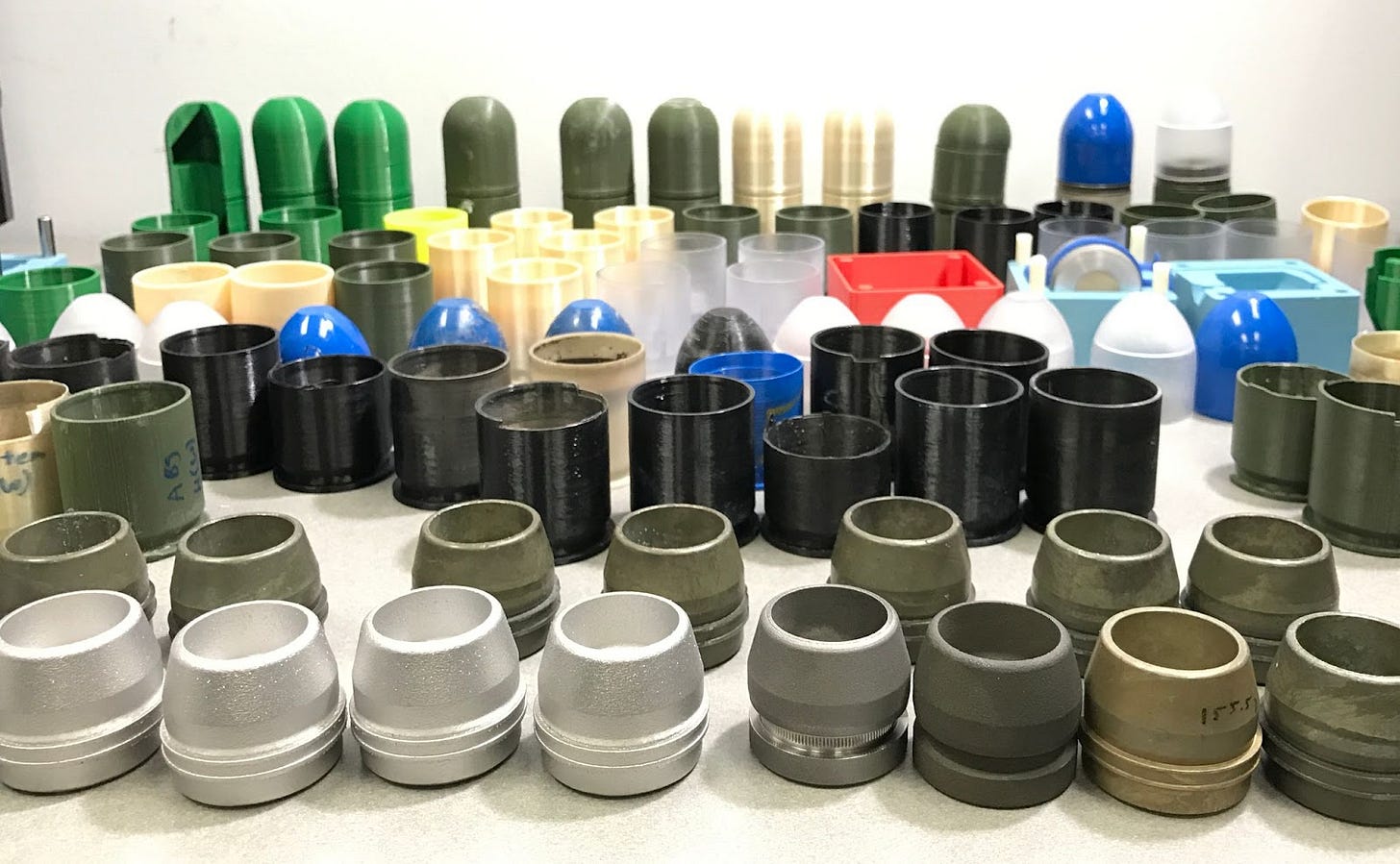
To call 3D printing or additive manufacturing a technology would be a misnomer. What binds together disparate techniques like directed energy deposition and material extrusion is not any technical commonality or tradition of knowledge, but a shared thesis on the organization of assembly lines and manufacturing supply chains. Namely, the thesis that a single computer able to manipulate matter is organizationally superior, or at least preferable in certain contexts, to the multiple separate assembly lines, facilities, and workers who would be necessary to manufacture the same component. In the extreme, one can imagine a device like the classic “replicator” in Star Trek, a fictional machine that can essentially zap any object into existence at the touch of a button.
This science-fiction idea was and remains the implicit promise of the term “3D printing,” which has nothing to do with printing ink on paper, but effectively conveys the instantaneity and customization of printing on paper and posits that this could be done with physical objects as well. For better or worse, this highly speculative and somewhat misleading idea has nevertheless proved highly appealing to investors, the media, and the numerous people with a casual interest in new technology, which is why synthetic food developers now say they are “3D printing meat,” even though the techniques behind that industry have even less to do with vat photopolymerization or powder bed fusion. Such marketing is however a double-edged sword, which can clearly be seen in the spectacularly falling valuations of 3D printing companies over the last decade.
The term “additive manufacturing” is a more formal and sober umbrella term, but ultimately no less of a marketing term that still groups together completely disparate techniques. With its viability for mass production still questionable, advocates of additive manufacturing have emphasized that it can reduce material consumption and improve the efficiency of vehicles using fewer parts. This is designed to garner approval from those who value ESG metrics. By emphasizing sustainability, companies are arguing their technology is ideal for a world with less overall consumption of manufactured goods. The claim is even made that additive manufacturing is inherently less wasteful of resources than “subtractive” manufacturing, because it doesn’t need to cut or shave off material.
These “sustainability” arguments are a mix of cynical and nonsensical, but the case that 3D printing techniques can streamline manufacturing processes and thus reduce organizational complexity is perhaps the core growth promise for the whole industry. The conceptual case for using 3D printers for idiosyncratic one-off uses, whether for out-of-stock, broken, prototype, or necessarily-customized parts, is obvious. But the vast majority of manufacturing will always necessarily be standardized to achieve economies of scale and there is little reason to think that the layering techniques of 3D printing will specifically prove, by and large, to be the most economical and efficient; on the contrary, there are plenty of reasons to think they will not, whether due to speed, material costs, defects, subpar structural integrity, or energy usage. Building cars with presses seems like it will always fundamentally make more sense than building them by squeezing metal through a tiny nozzle, no matter how advanced the technology gets.
But reducing complexity has its own economic utility to an individual company, factory, or manager, because it means fewer people to manage, fewer machines that can break down, and fewer suppliers to deal with. If a part that requires twenty different components, with their own assembly lines and supply chains, can be replaced by a single 3D-printed part made by a single machine, this is often not just less complex but also actually cheaper and more efficient. The 3D printer is a piece of technological complexity that displaces the need for a certain amount of organizational complexity. The idea that 3D printing will lead to a revolution in decentralized manufacturing is ultimately just the extreme version of this real step towards commodification of organizational complexity.
The precise limit of how far 3D printing can go in the global manufacturing base is ultimately unknowable and will depend both on advances in various techniques and a degree of institutional reform at manufacturers to integrate these new techniques in an economical way. But there is perhaps good reason to think that the current crop of companies in the industry are far more like research projects pretending to be companies, like Boston Dynamics, rather than nascent leaders in a vast new profitable industry. Though they have advanced different techniques to the present state of the art, they will perhaps never figure out the high-growth business model for 3D printing, if such a model can even exist for what are really a number of technical traditions of knowledge with completely different use cases. The idea that supply chains can be replaced with big complex machines may ultimately not be monetizable by anyone.
Tasha Keeney, “3D Printing Market: Analysts Are Underestimating the Future,” Ark Invest, April 20, 2016, https://ark-invest.com/articles/analyst-research/3d-printing-market.
“Additive Manufacturing Industry Grew 23 Percent in 2022 to $13.5B Reports SmarTech Analysis; Projects $25B by 2025,” PR Newswire, March 21, 2023, https://www.prnewswire.com/news-releases/additive-manufacturing-industry-grew-23-percent-in-2022-to-13-5b-reports-smartech-analysis-projects-25b-by-2025--301776749.html#:~:text=Even%20in%20the%20face%20of,20%25%2C%20to%20%247.3B.
Olena Yurchenko, et al. “CNC Machinery 2.0,” Economic security council of Ukraine, November, 2023,
https://reb.org.ua/storage/220/cnc-machines-2-0-website.pdf.
Dave Gershgorn and Signe Brewster,“The Best 3D Printer,” The New York Times, January 22, 2024, https://www.nytimes.com/wirecutter/reviews/best-home-3d-printer.
Ben Landau-Taylor and Oberon Dixon-Luinenburg, “Machine Tools,” Bismarck Analysis, February, 2020, https://www.bismarckanalysis.com/Machine_Tools_Case_Study.pdf.
David Rodríguez, “History of Additive Manufacturing. Part I,” Tesellated, July 16, 2022, https://tessellated.eu/en/blog/history-of-additive-manufacturing-part-i.
“US5121329A: Apparatus and method for creating three-dimensional objects,” Google Patents, 2024, https://patents.google.com/patent/US5121329A/en.
“DE2263777A1,” Google Patents, 2024,
“Current research and industrial application of laser powder directed energy deposition,” The International Journal of Advanced Manufacturing Technology, January 26, 2022,
https://link.springer.com/article/10.1007/s00170-021-08596-w.
“Powder bed fusion,” Loughborough University, 2024, https://www.lboro.ac.uk/research/amrg/about/the7categoriesofadditivemanufacturing/powderbedfusion.
Tia Vialva, “Carl Deckard, the inventor of SLS, passes away,” 3D Printing Industry, January 6, 2020, https://3dprintingindustry.com/news/carl-deckard-the-inventor-of-sls-passes-away-166853.
“DMLS – Development history and state of the art,” EOS, September 21, 2004, https://www.i3dmfg.com/wp-content/uploads/2015/07/History-of-DMLS.pdf.
David Svetlizky, “Laser-based directed energy deposition (DED-LB) of advanced materials,” Materials Science and Engineering: A, April 18, 2022,
https://www.sciencedirect.com/science/article/abs/pii/S0921509322003744.
Ziyad Smoqi, “Closed-loop control of meltpool temperature in directed energy deposition,” Materials & Design, March, 2022,
https://www.sciencedirect.com/science/article/pii/S0264127522001290.
Alex Knapp and Jemima McEvoy, “Relativity Space Launches Its First 3D-Printed Rocket, But Fails To Reach Orbit,” Forbes, March 22, 2023, https://www.forbes.com/sites/alexknapp/2023/03/22/relativity-space-3d-printed-rocket-launch/?sh=6d8b2a3a539a.
Elisebeth Peterson, “What is Laminated Object Manufacturing?” Live Science, October 9, 2013, https://www.livescience.com/40310-laminated-object-manufacturing.html.
Katelyn Arnold, “AM 101: What is Ultrasonic Additive Manufacturing?” Additive Manufacturing, June 16, 2022, https://www.additivemanufacturing.media/kc/what-is-additive-manufacturing/articles/am-101-ultrasonic-additive-manufacturing.
“Binder Jetting,” Loughborough University, 2024, https://www.lboro.ac.uk/research/amrg/about/the7categoriesofadditivemanufacturing/binderjetting.
“The Strongest Materials For 3D Printing,” Xometry Europe, November 24, 2021, https://xometry.eu/en/10-strongest-materials-for-3d-printing.
Eric Dustman, et al. “Metals 3D printing,” Strategy&, 2019, https://www.strategyand.pwc.com/gx/en/insights/2019/metals-3D-printing/metals-3d-printing.pdf.
Ibid.
“Technology overview for ceramic Additive Manufacturing,” Ampower, https://ampower.eu/infographics/ceramic-additive-manufacturing.
“From prototyping to mass production: the immediacy of 3D Printing,” Roboze, https://www.roboze.com/en/resources/from-prototyping-to-mass-production-the-immediacy-of-3d-printing.html.
“Task Force Report – 3D in Autorepair,” 3D in Autorepair, October 3, 2023, https://3dinautorepair.com/2023/10/03/task-force-report.
Tiffany Hsu, “3-D Printed Gun Advocate Cody Wilson Quits Company He Founded,” The New York Times, September 25, 2018, https://www.nytimes.com/2018/09/25/business/printed-gun-cody-wilson-defense-distributed.html.
“Align Technology Announces Third Quarter 2023 Financial Results,” Investors | Align Technology, October 25, 2023, https://investor.aligntech.com/news-releases/news-release-details/align-technology-announces-third-quarter-2023-financial-results.
Joris Peels, “What Align's Acquisition of Cubicure Means for Dental 3D Printing,” 3DPrint.com, September 13, 2023, https://3dprint.com/303306/what-aligns-acquisition-of-cubicure-means-for-dental-3d-printing.
Steve Banker, “3D Printing Revolutionizes the Hearing Aid Business,” Forbes, October 15, 2013, https://www.forbes.com/sites/stevebanker/2013/10/15/3d-printing-revolutionizes-the-hearing-aid-business/?sh=75d914be5ef2.
“Annual Report 2021/22," Sonova, https://report.sonova.com/2022/en/hearing-instruments-business.
Travis M. Hessman, “The Unassuming King of 3-D Printing,” IndustryWeek, October 2, 2014, https://www.industryweek.com/technology-and-iiot/article/21964406/the-unassuming-king-of-3d-printing.
Davide Sher, “GE Aviation ships 100,000th 3D printed nozzle tip,” VoxelMatters, August 19, 2021, https://www.voxelmatters.com/ge-aviation-ships-100000th-3d-printed-nozzle-tip.
Eric Tegler, “GE Aviation Hopes Its New Engine Will Be A Catalyst In The Turboprop Market,” Forbes, November 26, 2021, https://www.forbes.com/sites/erictegler/2021/11/26/ge-aviation-hopes-its-new-engine-will-be-a-catalyst-in-the-turboprop-market/?sh=74736ea567fe.
“GE reveals future 3D Printing plans in exclusive US facility tour,” Foundry Planet, October 27, 2022, https://www.foundry-planet.com/d/ge-reveals-future-3d-printing-plans-in-exclusive-us-facility-tour.
Kubi Sertoglu, “WAAM3D launches new RoboWAAM 3D printer, Sciaky breaks deposition rate record,” 3D Printing Industry, June 10, 2022, https://3dprintingindustry.com/news/waam3d-launches-new-robowaam-3d-printer-sciaky-breaks-deposition-rate-record-210529.
In partnership with the Italian Idra Group, Tesla has pioneered high-pressure die casting to build subcomponents of its car body. Its 400-ton “Giga Press” injects molten aluminum into a mold at high pressure and uses a clamping strength of 9000 tons to form the body part, which is subsequently cooled and ready for assembly. This technology means a car body can be assembled from three parts instead of hundreds. The giga-press has a cycle time of 120 seconds, meaning 30 castings per hour, or 500 casts of an automotive body part over three 8-hour shifts. Each chassis weighs over 100 kilograms, meaning an effective deposition rate of 3000 kilograms per hour.
Umar Shakir, “Tesla’s new car-building process could be a huge industrial breakthrough,” The Verge, September 14, 2023, https://www.theverge.com/2023/9/14/23873345/tesla-gigapress-gigacasting-manufacturing-breakthrough.
“Metals 3D printing,” Strategy&, 2019, https://www.strategyand.pwc.com/gx/en/insights/2019/metals-3D-printing/metals-3d-printing.pdf.
“Why 3D Printing Is Expensive As Compared To Conventional Manufacturing?” 3D Incredible, November 8, 2022, https://3dincredible.com/why-3d-printing-is-expensive-as-compared-to-conventional-manufacturing.
Joris Peels, “RIP 3D Printing: The Cart Before the Horse,” 3DPrint.com, November 3, 2023, https://3dprint.com/304336/rip-3d-printing-the-cart-before-the-horse.
Lucas Carolo, “3D Printer Material Cost of 2023,” All3DP, June 1, 2023, https://all3dp.com/2/3d-printer-material-cost-the-real-cost-of-3d-printing-materials.
“Wholesale Titanium Prices Per Kg," Alibaba, https://www.alibaba.com/showroom/titanium-price-per-kg.html.
Juan Silva, “Comparative life cycle inventory of CNC machining and power bed fusion additive manufacturing,” Aalto University, December 29, 2022, https://aaltodoc.aalto.fi/server/api/core/bitstreams/f1852a62-130c-4404-836e-681e4ce9deb9/content.
Nate Barnett, Dave Costenaro and Ingrid Rohmund, “Direct and Indirect Impacts of Robots on Future Electricity Load,” American Council for an Energy Efficient Economy, 2017, https://www.aceee.org/files/proceedings/2017/data/polopoly_fs/1.3687904.1501159084!/fileserver/file/790278/filename/0036_0053_000029.pdf.
Martin Baumers, Matthias Holweg and Jonathan Rowley, “The economics of 3D Printing: A total cost perspective,” Institute for Manufacturing (IfM), https://www.ifm.eng.cam.ac.uk/uploads/Research/TEG/3DP-RDM_Total_cost_report.pdf.
Jordan Taylor, “How it works? Metal powders (or multiple metal types, for in-situ alloying) are blown in an argon gas stream, to prevent oxidisation, to a laser focal point, which melts & deposits the powder at over 2700K, and then cools at 10,000-1,000,000 degrees...” X, August 29, 2023,
https://twitter.com/Jordan_W_Taylor/status/1696502613540254052
.
“Real-time crack detection in Directed Energy Deposition (DED) produced components,” Diamond Light Source, 2023, https://www.diamond.ac.uk/industry/Industry-News/Latest-News/2023/Synchrotron-Industry-News-crack-detection-in-directed-energy-deposition-components.html.
Michael Liu, et al. “A Review of the Anomalies in Directed Energy Deposition (DED) Processes & Potential Solutions - Part Quality & Defects," Procedia Manufacturing, 2021, https://doi.org/10.1016/j.promfg.2021.06.093.
“3D Systems Reports Fourth Quarter and Full Year 2022 Financial Results,” 3D Systems, February 28, 2023, https://www.3dsystems.com/press-releases/3d-systems-reports-fourth-quarter-and-full-year-2022-financial-results.
“3D Systems (DDD) - Market capitalization,” Companies Market Cap, https://companiesmarketcap.com/3d-systems/marketcap.
James Manyika, et al. “Disruptive technologies: Advances that will transform life, business, and the global economy,” McKinsey, May 2, 2013, https://www.mckinsey.com/~/media/mckinsey/business%20functions/mckinsey%20digital/our%20insights/disruptive%20technologies/mgi_disruptive_technologies_full_report_may2013.pdf.
Michael Molitch-Hou, “A Look at ARK’s 3D Printing Fund, “PRNT”,” 3DPrint.com, December 6, 2021, https://3dprint.com/287324/a-look-at-arks-3d-printing-fund-prnt.
Michael Molitch-Hou, “3D Printing to Reach $18.8B in Revenues in 2023,” 3DPrint.com, December 5, 2023, https://3dprint.com/305519/3d-printing-to-reach-18-8b-in-revenues-in-2023.
Michael Molitch-Hou, “Billionaire Buys 7% of Desktop Metal as Activist Investor,” 3DPrint.com, June 11, 2023, https://3dprint.com/300899/billionaire-buys-7-of-desktop-metal-as-activist-investor.
Oliver Johnson, “ISS recommends Stratasys shareholders reject Desktop Metal merger, says 3D Systems deal offers more value,” TCT Magazine, September 21, 2023, https://www.tctmagazine.com/additive-manufacturing-3d-printing-news/latest-additive-manufacturing-3d-printing-news/proxy-advisor-opposes-stratasys-merger-with-desktop-metal-and-says-3d-systems-deal-offers-more-value.
Amy Feldman, “His Bosses Rejected His Idea. Then Hans Langer Became A Billionaire From His Plan For Giant 3-D Printers,” Forbes, March 18, 2019, https://www.forbes.com/sites/amyfeldman/2019/03/18/his-bosses-rejected-his-idea-then-hans-langer-became-a-billionaire-from-his-plan-for-giant-3d-printers/?sh=460e42383669.
Ibid.
“Profile: Hans Langer," Forbes, 2024, https://www.forbes.com/profile/hans-langer/?sh=122f1ede47bf.
Amy Feldman, “Marie Langer Took Charge Of Her Billionaire Family’s 3D Printing Firm Months Before Covid-19 Struck. Here’s How She Navigated The Downturn—And Her Plan For The Future,” Forbes, March 15, 2021, https://www.forbes.com/sites/amyfeldman/2021/03/15/marie-langer-took-charge-of-her-billionaire-familys-3d-printing-firm-months-before-covid-19-struck-heres-how-she-navigated-the-downturn-and-her-plan-for-the-future/?sh=252fcbec779d.
Sagar Joshi, “3D Printing Statistics: 69 Facts and Trends to Follow in 2023,” Learn G2, July 19, 2023, https://learn.g2.com/3d-printing-statistics.
Kickstarter page archived here: “Bambu Lab X1: CoreXY Color 3D Printer with Lidar and AI,” Kickstarter, Archive.today, September 29, 2022, https://archive.is/Kfc2j#selection-611.0-611.55.
“BLT reports 66% growth with record revenues of $140M in 2022,” Metal AM, May 15, 2023, https://www.metal-am.com/blt-reports-66-growth-with-record-revenues-of-140m-in-2022.
Vanesa Listek, “Analyzing Farsoon: A Closer Look at the Recent IPO of A Chinese 3D Printing Leader,” 3DPrint.com, May 31, 2023, https://3dprint.com/300568/analyzing-farsoon-a-closer-look-at-the-recent-ipo-of-a-chinese-3d-printing-leader.
Rushabh Haria, “China state Action Plan aims to make 3D printing worth $3 billion by 2020,” 3D Printing Industry, December 14, 2017, https://3dprintingindustry.com/news/china-action-plan-3d-printing-3-billion-2020-126119.